A mainstay of manufacturing and production, Material Requirements Planning (MRP) gives companies an organized way to handle their components, materials, and production schedules. It is an essential instrument for guaranteeing that the appropriate resources are accessible in the appropriate quantities and at the appropriate times to support manufacturing procedures and satisfy consumer demand.
Fundamentally, MRP uses production scheduling and data analysis methods to ascertain the ideal amount and timing of materials required for manufacturing. MRP systems help firms plan and carry out production activities more effectively by assessing things like the bill of materials (BOM), current inventory levels, and the master production schedule. This proactive strategy lowers the cost of keeping inventory on hand, speeds up production, and improves overall operational effectiveness for firms.
When appropriately applied, these MRP system features could result in lower costs and increased output. However, correct data entry is required for an MRP system to effectively enhance production operations. Ordering and planning will be distorted by incorrectly entered numbers.
What is MRP ?
To manage manufacturing operations, organizations employ Material Requirements Planning (MRP), a production planning and inventory control system. Its goal is to minimize inventory levels and expenses while guaranteeing that components and materials are available for manufacturing.
To ascertain the amount and timing of materials required for production, MRP examines the bill of materials (BOM), current inventory levels, and master production schedule.
MRP provides suggestions for acquiring or generating resources to fulfill production needs based on this research.
1. Master Production Schedule (MPS): A comprehensive plan outlining how much and when finished goods are to be produced over a given period of time.
2. Bill of Materials (BOM): A list that includes the amounts and interrelationships of all the materials and components needed to make a final product.
3. Inventory Records: Details on the amount of materials and components ordered, lead times, and current inventory levels.
4. Materials Needed Planning Logic: Algorithms and computations that leverage the MPS, BOM, and inventory records to determine material requirements.
Tools and Software for MRP
To assist Material Requirements Planning (MRP) procedures in manufacturing and production settings, a number of hardware and software technologies are available. ERP (enterprise resource planning) systems are unique in that they combine MRP components to provide a uniform platform for managing materials, production schedules, and inventory levels. Numerous functionalities are available in these systems, which include SAP ERP, Oracle ERP Cloud, and Microsoft Dynamics 365, to optimize MRP processes in addition to other company operations.
Specialized capabilities for MRP are offered by dedicated MRP software, which may analyze inventory levels, bill of materials (BOM), and demand projections to provide suggestions for production scheduling and material purchase. MRP by MIE Solutions, Plex Systems, and NetSuite MRP are a few examples. For the purpose of controlling resources and production schedules, these technologies include sophisticated planning and optimization features.
Integrating MRP with shop floor processes is made possible in large part by Manufacturing Execution Systems (MES). Businesses may effectively manage material usage, work orders, and production scheduling by utilizing MES solutions such as Siemens Opcenter, IQMS MES, and Apriso MES, which offer real-time visibility into production processes. MRP features are also included in certain MES systems to smoothly integrate production planning with shop floor operations.
Moreover, tools for monitoring and controlling inventory levels are provided by inventory management software programs like TradeGecko, inFlow Inventory, and Fishbowl Inventory. By integrating these technologies with MRP systems, inventory replenishment procedures can be automated and real-time visibility into inventory levels can be obtained. In addition to MRP procedures, supply chain planning (SCP) systems and production scheduling software offer sophisticated planning and optimization features to match production schedules with material requirements and customer demand.
The MRP’s Business Value
Material Requirements Planning (MRP) adds value to businesses by helping to efficiently satisfy customer demand, optimize inventory management, and expedite manufacturing operations. Businesses that use MRP systems can reap the following major advantages:
Better Inventory Management
By guaranteeing that supplies are accessible when needed for production, MRP helps companies to maintain ideal inventory levels. Businesses can decrease excess inventory, save carrying costs, and avoid stockouts by aligning material purchases with production schedules and demand predictions.
Enhanced Production Efficiency
By giving firms visibility into material requirements and production schedules, MRP helps organizations simplify their production processes. In the end, this improves total production efficiency by helping organizations to plan and carry out production tasks more effectively, decrease downtime, and maximize resource use.
Enhanced Customer Satisfaction
MRP assists companies in regularly meeting customer demand and delivering products with shorter lead times by guaranteeing that resources are accessible for manufacturing and orders are fulfilled on time. Increased client pleasure, loyalty, and repeat business result from this.
Cost Reduction
By optimizing purchasing and production plans, MRP helps firms cut waste and expenses related to stockouts, expediting, and inventory holding. By coordinating the procurement of materials with production schedules and demand projections, companies can reduce wasteful spending and increase profitability.
Conclusion | Exploring Material Requirements Planning (MRP) in Business Operations: A Mastery of Efficiency
Finally, Material Requirements Planning (MRP) provides an efficient way to manage materials, manufacturing schedules, and customer demand, making it a fundamental component of contemporary corporate operations. Businesses may satisfy consumer demands precisely, improve manufacturing processes, and optimize inventory management by utilizing MRP systems. Businesses may make well-informed decisions, cut expenses, and adjust to changing market conditions because to the strategic alignment that MRP provides. This eventually leads to operational excellence and the maintenance of competitive advantage.
Material requirements planning, or MRP, is a mastery of efficiency that is essential in today’s fast-paced and cutthroat business environment. Businesses may negotiate complexity, grab opportunities, and achieve operational excellence by utilizing MRP systems, positioning themselves for long-term success and expansion in the dynamic marketplace.
image courtesy
Photo by lil artsy, Photo by Pixabay
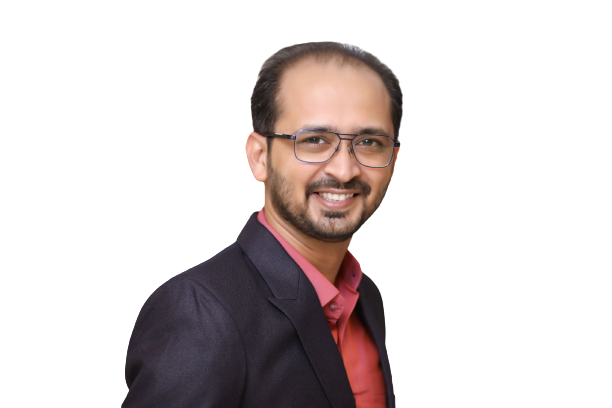