Harnessing Customized Solutions to Drive Agility and Efficiency in Manufacturing Operations
In the dynamic landscape of manufacturing, where market demands, technological advancements, and operational challenges are constantly evolving, the ability to adapt to change is essential for sustainable success. Traditional manufacturing approaches often struggle to keep pace with the rapid shifts in customer preferences, supply chain disruptions, and emerging industry trends. In response to these challenges, forward-thinking manufacturers are embracing agile principles and seeking innovative solutions to enhance their adaptability and responsiveness.
“Adapting to Change: Custom MRP Software for Agile Manufacturing” explores the intersection of agility and technology in modern manufacturing environments. This topic delves into the critical role of Material Requirement Planning (MRP) software customized for agile manufacturing processes, offering insights into how tailored solutions can empower manufacturers to thrive in a rapidly changing landscape.
In this exploration, we will examine the challenges faced by manufacturers in adapting to change, from fluctuating demand patterns to the need for rapid production adjustments. We will then delve into the concept of agile manufacturing and its principles of flexibility, collaboration, and continuous improvement. From there, we will transition to the role of MRP software in facilitating agile operations, highlighting the benefits of customization in meeting the unique needs and challenges of agile manufacturing environments.
Adapting to Change: The Evolution of Agile Manufacturing
Agile manufacturing is a production methodology that emphasizes flexibility, responsiveness, and adaptability to meet changing customer demands and market conditions. Unlike traditional manufacturing approaches that prioritize large-scale production runs and long lead times, agile manufacturing focuses on quick response times, customization, and continuous improvement.
Key principles of agile manufacturing include:
Flexibility: Agile manufacturing enables rapid adjustments to production processes, allowing companies to quickly respond to changes in demand, supply chain disruptions, or emerging market trends.
Customer-Centricity: Agile manufacturing places a strong emphasis on understanding and meeting customer needs by offering customized products, shorter lead times, and enhanced quality.
Collaboration: Collaboration and communication among cross-functional teams are essential in agile manufacturing environments to facilitate rapid decision-making and problem-solving.
Innovation: Agile manufacturing fosters a culture of continuous improvement and innovation, encouraging experimentation, creativity, and the adoption of new technologies to enhance productivity and competitiveness.
Lean Principles: Agile manufacturing often incorporates lean manufacturing principles to eliminate waste, reduce inventory levels, and optimize production processes.
Optimizing Production: The Role of Material Requirement Planning (MRP)
Material Requirement Planning (MRP) is a systematic approach to managing the materials needed for production within a manufacturing environment. The primary objective of MRP is to ensure that the right materials are available in the right quantities at the right time to support production schedules and meet customer demand.
Key components of MRP include:
Bill of Materials (BOM): A comprehensive list of all components and materials required to manufacture a product, including quantities and specifications.
Inventory Management: Tracking and managing inventory levels to ensure adequate stock of materials while minimizing excess inventory and associated carrying costs.
Master Production Schedule (MPS): A detailed plan that specifies the quantity and timing of production for each finished product, taking into account customer orders, forecasted demand, and production capacity.
Material Requirements Planning (MRP): The process of determining the materials needed for production based on demand forecasts, production schedules, and inventory levels.
MRP systems typically utilize computer software to automate the planning and scheduling processes, enabling manufacturers to optimize resource allocation, minimize production lead times, and improve overall efficiency.
Tailored Efficiency: Unlocking Potential with Custom Software Solutions
Custom software solutions are uniquely designed and developed software applications that cater to the specific needs, requirements, and goals of an organization or business. Unlike off-the-shelf software, which offers generic features and functionalities, custom software solutions are built from scratch or customized extensively to align perfectly with the unique workflows, processes, and objectives of the organization.
Key aspects of custom software solutions include:
-
Personalization: Custom software solutions are tailored to address the specific challenges and requirements of the organization, ensuring that every aspect of the software is designed to fit its unique needs and preferences.
-
Scalability: Custom software solutions are designed to grow and evolve with the organization, allowing for easy integration of new features, modules, or functionalities as the business expands or its requirements change over time.
-
Integration: Custom software solutions can seamlessly integrate with existing systems, applications, and infrastructure within the organization, ensuring compatibility and interoperability across the entire IT ecosystem.
-
Flexibility: Custom software solutions offer flexibility in terms of design, architecture, and technology stack, allowing for greater customization and adaptability to changing business requirements.
-
Support and Maintenance: With custom software solutions, organizations have the option to receive ongoing support and maintenance services from the development team, ensuring that the software remains up-to-date, secure, and optimized for performance.
Overall, custom software solutions empower organizations to streamline processes, enhance efficiency, and gain a competitive edge by leveraging technology that is tailor-made to fit their unique needs and objectives.
Optimizing Operations: Driving Efficiency for Organizational Success
Operational efficiency is the linchpin of organizational success, serving as the backbone upon which businesses can thrive in today’s fast-paced and competitive landscape. At its core, operational efficiency involves the optimization of processes, resources, and systems to achieve maximum productivity and effectiveness. This entails identifying and eliminating inefficiencies, streamlining workflows, and ensuring that resources are allocated judiciously to minimize waste and maximize output.
By focusing on operational efficiency, businesses can achieve a myriad of benefits. Firstly, improved efficiency translates to cost savings as it reduces overhead expenses, eliminates unnecessary expenditures, and enhances resource utilization. This, in turn, can lead to increased profitability and financial stability for the organization. Moreover, operational efficiency enables businesses to deliver products and services to customers more quickly, accurately, and reliably, thereby enhancing customer satisfaction and loyalty.
Furthermore, operational efficiency fosters a culture of continuous improvement within the organization. By constantly seeking out ways to optimize processes and workflows, businesses can adapt more readily to changing market conditions, technological advancements, and customer preferences. This agility and adaptability are crucial for businesses to remain relevant and competitive in an ever-evolving marketplace.
Additionally, operational efficiency plays a pivotal role in driving innovation and fostering growth. By streamlining operations and freeing up resources, businesses can allocate more time and energy towards research, development, and innovation. This enables them to stay ahead of the curve, anticipate future trends, and capitalize on emerging opportunities, ultimately fueling long-term growth and success.
conclusion | Adapting to Change: Custom MRP Software for Agile Manufacturing
In conclusion, the adoption of custom Material Requirement Planning (MRP) software for agile manufacturing represents a strategic imperative for businesses looking to thrive in an ever-changing environment. By embracing tailored solutions that are specifically designed to meet the unique needs and challenges of agile manufacturing processes, organizations can unlock new levels of efficiency, flexibility, and responsiveness. Through the integration of custom MRP software, businesses can streamline production workflows, optimize resource allocation, and adapt quickly to shifting market demands, ultimately gaining a competitive edge in the dynamic manufacturing landscape.
Moreover, the implementation of custom MRP software underscores a commitment to continuous improvement and innovation within the organization. By leveraging technology to automate and optimize production planning, scheduling, and inventory management processes, businesses can foster a culture of agility and adaptability that is essential for long-term success. As market dynamics evolve and customer preferences change, organizations equipped with custom MRP software are better positioned to anticipate challenges, capitalize on opportunities, and drive sustained growth and profitability in an increasingly competitive marketplace.
image courtesy
Photo by Pixabay, Photo by Anamul Rezwan, Photo by Christina Morillo, Photo by Vlada Karpovich
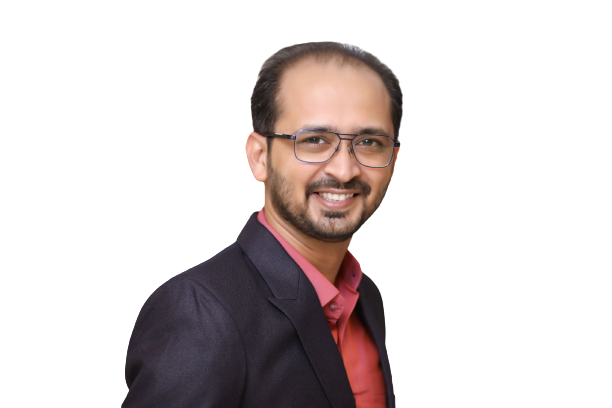